Part 1: Contamination
One of the most common issue that fortunately can be addressed during maintenance is contamination. Power Electronical presents to you a thorough description expressing this issue – cause, effects, its detection and solution through a series of articles. This is first part that talks about different type of contamination, how machines get contaminated and what are its effects.
There have been several surveys into industrial motor failures. The EPRI survey in 1983, IEEE survey in 1985 and one again in 1995 indicated that most failing component was bearings (nearly around 40 – 60 %) followed by stator windings (16 – 30 %).
Bearing failures is a different study altogether and besides issues of contamination of grease and abrasion/spall on the parts in contact (inner/outer race and balls/rollers) which are direct in nature, any other mechanical issue with motor such as unbalance, bad foundation, alignment problems with load etc., ultimately manifests on the bearing causing it to fail. However, such bearing defects can be detected at incipient stage, ahead in time using various techniques like vibration monitoring, motor line current spectrums, acoustic emissions, spike energy detection. Also, such bearings can be replaced easily, and downtimes associated are not high. Activity can be quickly undertaken during a planned outage.
Stator windings – second most failing component requires elaborate techniques to predict or detect signs of failures. Also, the cost of repair is high and so are downtime requirements. If it is a top bar failure, it could take up a few days, but if it is failure of bottom bar, repair times could take several weeks. Also, this largely depends on availability of spare stator bars and its preservation in good condition.
Based on this, there have been further study on the contributors of failures and the famous acronym of T.E.A.M stresses (Thermal, Electric, Ambient, Mechanical). It may also be noted that the stresses are seldom acting by itself but working together giving more weightage to meaning of the word – “Team”. Let me explain with an example – Partial discharges are small arcs in localized zones and contributes to “Electric Stress”, typically seen in 6.6 kV and above rated motors/generators. Such PD may occur in small air gaps between coil and core in straight portion of the slots where the coils/bars are inserted. It is called as “Slot Discharges”. This causes erosion of anti-corona paint or tape on coil sides and resin content of epoxy-mica tapes. The coil thickness is marginally reduced, and coil vibrates in slots causing “Mechanical Stress”. Now, both stresses act together – Electro-Mechanical Stress. Similarly, there are Thermo-Mechanical Stress – vibration causing friction of parts and increasing its temperatures.
In this article, we focus on the A = Ambient Stress, which means the environmental factors or simply put – contamination.
Motors and generators are often installed at locations that could be broadly classified as “indoor” or “outdoor”. While it is easy to perceive that outdoor locations are exposed to dirt, dust, rain which can find its way inside the machine, indoor locations are generally in good condition as they could be clean generator floors or generally has good housekeeping around the application. Is it so? Also, what if the application mandates installation of machine in corrosive atmospheres e.g., coal mining application, saw-mills.

What are contaminants?
So generally external particulate matter that enters inside the machine are “contaminants”. They spread mainly along the stator overhang areas as it has relatively larger surface area and closer to the points of entry of these contaminants. In case these particles are in excess in the atmosphere around the motor, it may spread into the slot areas, stator core, rotor core, inside the rotor through open areas around the shaft and through air gaps between stator and rotor.
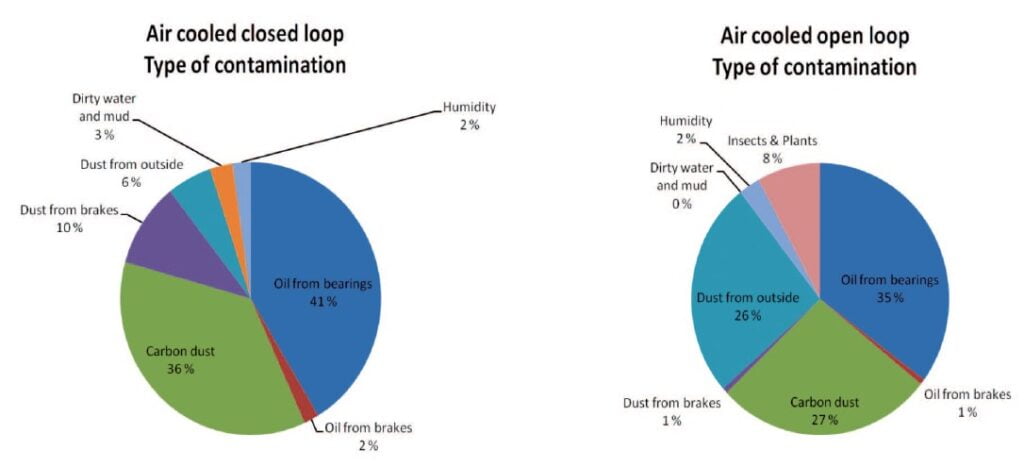
Carbon dust, dust from brakes and dust from outside make for nearly 50 % of all possible contaminants. Most industrial sites have huge tract of lands and open spaces on which the plant is built. Construction work, unpaved roads, sand/mud tracts on roadsides, fields, sand etc. result in lot of dust – which is particulate matter of sizes of 10 micron that remain suspended in air and carried by winds. Smokes from chimneys, any fire burning around results in fine particles less than 2.5 microns.
Carbon particles are found in environment due to smoke, fumes etc. In power plants, there is coal handling plant which can be a potential source of coal dust. Some sources are really close to machine itself – e.g., carbon brush assemblies such as in slip-ring induction motors/dc motors or exciters.
Some pictures as below show light to significant dust contaminants on stator windings (overhangs):
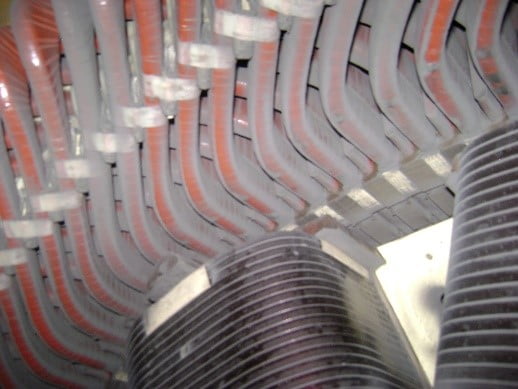

There are often the exceptional cases of broken filter that can cause heavy dust contamination as in this picture where the complete overhangs are covered in layers of dust (2 pictures below- Dust contamination-01 & 02). Another common finding in cement plants is cement dust (2 pictures below- Cement contamination-01 & 02)




Carbonized dust as shown below would be more harmful due to its conductive nature. Rotating machines have fans or fan blades that suck and guide air into the motor for purpose of cooling. It is thus imperative that dust/carbon particles get sucked into the motor from the air due to fan suction.


The other most common contaminant indicated is “oil from bearings”. Note that larger motors/generators – having heavy weight and high-speed use sleeve bearings (journal bearings) that use oil for lubrication. The rotor rests/rotates on oil film in these bearings. Though it employs seals to avoid oil leakage, any damage to the seals, results in oil leakage or its spraying in mist form inside the machines and onto the windings. Smaller motors use anti-friction bearings (ball/roller), where the lubrication is grease. One of the most common reason for such bearing failures has been over greasing. Excessive grease is ejected out of the bearings and it contaminates the stator overhangs.


There can be a combination of carbon dust and oil on windings, which is typically common for generators. Often, this combination is hygroscopic in nature and will absorb “moisture” – yet another type of contaminant.



Often, there are these odd or rare cases of finding some different contaminants as shown in cases below. These extend from insects – dead or alive – most commonly spiders, but mosquitoes, dragonflies, bugs, beetles, roaches. This can extend to bigger animals like reptiles – lizards, snakes or rodents like mice (particular for idle units). Not to mention faecal matter of birds!


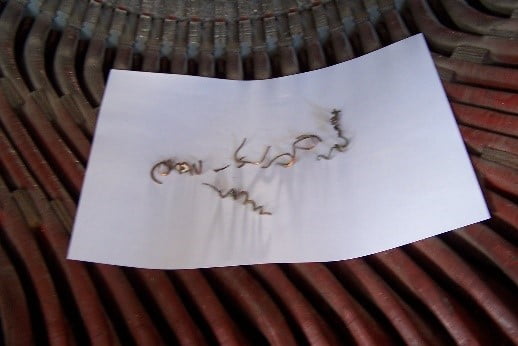
There are cases where metal filings or metallic dust have been found, probably due to some machining process in near vicinity.
Wood particles, saw dust, Paper particles, plastic etc, have also been found. In one case, probably human error that can be avoided, washers/nuts and in one odd case spare copper bars, wrapped in plastic found in terminal box. In India and many other countries have experienced heavy rainfall and flooding of plants. Machines submerged in flood waters are often found covered in sludge, mud, muck and need a complete overhaul treatment in a workshop.
Do these contaminants pose any risk?
It is true that maintenance personnel have known of machines with contamination running several years without any failures or performance issue. Also, present day global VPI type of insulated technology provides sealing and hence such surface level dust and moisture or even oil should not really affect the machine performance or reliability. Also, IR and PI values (will cover in detail in next part of the series) for such units are in exceptionally good/acceptable range. So, this question has lot of relevance.
For most machines with varnish layer on top or GVPI units, dust contaminants do not pose any immediate harm and are unlikely to cause any immediate failure. However, there are several secondary or indirect effects that can occur slowly and gradually over a long period of time it may create irreversible effects that can lead to failures. Let us understand some of these effects:
- Contaminants like dust and sand or even cement and saw dust while they are dry may not cause any damage by itself. However, in humid conditions, they absorb moisture and get soggy. This greatly affects the insulation and can aid partial discharges along the surface – also called “tracking”. It provides a capacitive path between stator bars of different phases or phase and ground parts and can cause “surface discharges” or “end-winding discharges”. Such discharges also may not cause an immediate failure. However, high energies associated at the microscopic tips of these discharges impinge on insulation material and can cause erosion of the resin or binding material. It can cause localized carbonization or pitting. The insulation material properties change, and it becomes conductive. It causes more of such discharges and damage cumulatively over time make insulation vulnerable to failure.
- The other secondary damage is that such contaminants clog the vent ducts and air paths. The contaminant layer on top of stator bar will prevent conduction of heat from stator bars to the colling medium – air or hydrogen. The windings run hotter than previous. It has been seen from Arrhenius chemical wear rate equation and curves that every 10 0C rise in temperature can reduce the insulation life by half. So even though such contaminants may not cause such a 10 0C temperature rise, any rise will cause the electron in insulation to oscillate rapidly and gain energy enough to break its valence bond. Its properties change gradually from good to moderate or bad dielectric, affecting insulation reliability and life.
- Surface varnish paints often crack in influence of heat or forces within the machine. Excessive contaminants can then find way inside these cracks and spread under the varnish layers. Thermal fatigue stresses in insulation due to cyclic temperature rise and fall such as due to start/stop or duty cycle of motor causes expansion and contraction forces between insulation tapes and between insulation and conductor. This leads to insulation delamination or tape separation. Often oil contaminants with moisture under such varnish layers can seep through the tape layers further into innermost layer. This is extremely dangerous situation as such contaminants remain trapped under insulation layers and cannot be removed during cleaning and secondly it extends ground potential closer to the copper conductor aiding “treeing” and flashovers.
So, while there are many intrinsic phenomena (inside insulation layers) that cannot be attended during maintenance outages. However, contamination can be removed and should be aimed for. It is known to provide an extension or at least sustain the life closer to designed life of insulation.